重力鋳造金型 は永久金型鋳造とも呼ばれ、鋳造金属部品の製造に使用される製造プロセスです。このプロセスでは、溶解した金属が重力の影響下で金型に注がれ、凝固して金型の形になります。金型は通常、鋼や鉄などの耐熱材料で作られており、耐久性があり長持ちするように設計されています。
重力鋳造の主な利点は、優れた寸法精度と表面仕上げを備えた高品質で複雑な部品を製造できることです。このプロセスは、鉄、鋼、ニッケルなどの高融点金属の鋳造に特に適しており、エンジン ブロック、ギア、その他の高強度部品の製造によく使用されます。
重力鋳造プロセスでは、熱衝撃を軽減し、ひび割れのリスクを最小限に抑えるために、通常、金型を予熱します。次に、溶かした金属を型に流し込み、凝固させて型の形にします。金属が固化したら、金型を取り外し、必要に応じて部品を仕上げて機械加工します。
重力鋳造は、高品質の部品を大量に生産できる、費用対効果が高く効率的な製造プロセスです。ただし、要求される仕様と基準を満たす部品を製造するには、高品質の金型を選択し、鋳造プロセスを慎重に管理することが重要です。
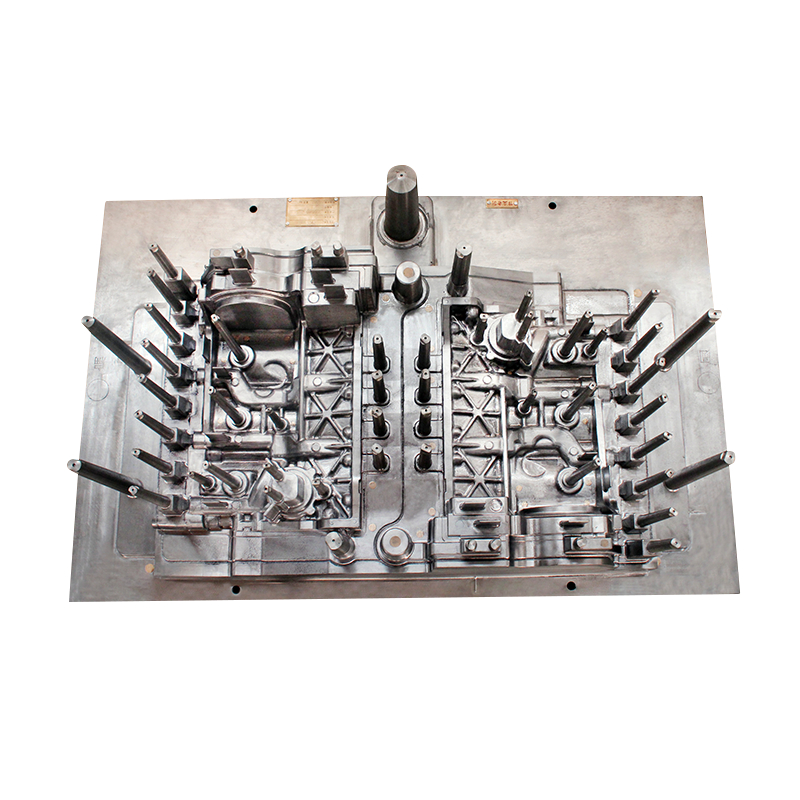
シリンダーブロック上型は、内燃機関の主要部品であるシリンダーブロックの上部を鋳造するための金型です。シリンダーブロックは、シリンダー、つまりピストンが上下に動くスペース、およびクランクシャフトやコネクティングロッドベアリングなどの他の重要なコンポーネントを含む大きな中空の鋳造品です。上金型は通常、金属製で、下金型と組み合わせて使用され、シリンダー ブロックを形成します。通常、2 つの金型は一緒にクランプされ、溶融金属がそれらの間のスペースに注がれ、そこで冷却されて固化してシリンダー ブロックが形成されます。鋳造プロセスが完了すると、金型が分離され、完成したシリンダー ブロックが取り出されます。